Robotic aluminum MIG welding utilizes automated systems to perform MIG (Metal Inert Gas) welding on aluminum components. Here’s an overview:
- Process Expertise: Aluminum MIG welding requires specialized knowledge due to aluminum’s properties like high thermal conductivity and susceptibility to oxidation. Robotic systems are programmed to manage these challenges effectively.
- Precision and Efficiency: Robots ensure consistent weld quality and precision, minimizing defects and optimizing production efficiency compared to manual welding.
- Equipment and Setup: The process involves selecting appropriate welding equipment, including robots with aluminum-specific torches, wire feeders, and shielding gas systems tailored for aluminum welding.
- Programming and Integration: Robots are programmed to execute precise weld paths, controlling parameters such as torch angle, speed, and weld bead characteristics. Integration with CAD/CAM systems aids in optimizing weld paths for complex aluminum components.
- Quality Assurance: Automated systems include sensors for real-time monitoring of welding parameters, ensuring adherence to quality standards and enabling adjustments as needed during production.
Robotic aluminum MIG welding offers significant advantages in industries requiring high-strength, lightweight aluminum components, such as automotive, aerospace, and marine sectors, ensuring consistent weld quality and productivity.
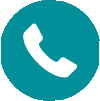
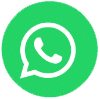
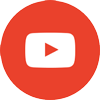