Robotic sheet metal welding involves the automated welding of thin metal sheets using robotic systems equipped with specialized welding tools. Here’s an overview of the process:
- Automation Benefits: Robotic welding offers precision and repeatability, crucial for maintaining consistent weld quality on thin sheet metal. It reduces variability compared to manual welding, ensuring higher productivity and fewer defects.
- Equipment Setup: The process begins with selecting appropriate robotic arms and welding equipment capable of handling thin sheet metals. This includes MIG (Metal Inert Gas) or TIG (Tungsten Inert Gas) welding systems tailored for sheet metal applications.
- Programming and Path Planning: Robots are programmed using CAD/CAM software to follow precise weld paths. This includes setting parameters such as welding speed, arc length, and torch angle to achieve optimal weld bead formation and strength.
- Fixture Design: Fixtures are designed to securely hold sheet metal parts in position during welding, ensuring dimensional accuracy and minimizing distortion caused by heat.
- Quality Control: Integrated sensors and vision systems monitor welding parameters in real-time, detecting deviations and ensuring weld quality meets specified standards. This real-time feedback allows for immediate adjustments during production.
- Safety and Efficiency: Robotic systems incorporate safety features such as protective barriers, light curtains, and emergency stop mechanisms to safeguard operators and equipment during welding operations.
Robotic sheet metal welding is widely used in industries such as automotive, aerospace, and electronics manufacturing, where precision, speed, and consistency are critical for producing high-quality components efficiently.
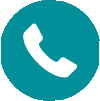
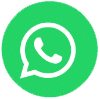
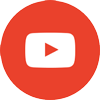